In the realm of materials testing, the assessment of grease consistency is crucial for various industrial applications, ranging from automotive to machinery lubrication. A grease penetrometer, a device designed to measure the consistency of grease, plays a pivotal role in this regard. This article delves into the workings of the grease penetrometer, explores the ASTM D217 standard, elucidates consistency, and penetration number, and provides insight into the significance of the penetrometer in grease analysis.
Lubrication plays an important role in any machine parts having relative motion. Grease is one of the lubricants but of semi-fluid or semi-solid type lubricant. Grease selection for a particular application is done by the grease penetration number measured by a grease penetrometer. To know more about grease penetration numbers, read the following sections.
Table of Contents
What is Grease?
Grease is a semi-fluid lubricant made of base oil and thickener. The measure of relative hardness of grease is referred to as a consistency number as per N.L.G.I (National Lubricating Grease Institute) a trade association that governs lubrication and related industry research.
Where do we use grease?
Grease is used where a continuous supply of oil cannot be retained/possible. e.g. Such as ball and roller bearings, chassis components of automobiles, and chains of mechanisms.
Ingredients of Grease
Grease is normally made up of the following components:
- Base Oil: Normally mineral oil, the synthetic fluid acts as base oil which is about 70-95% in grease content. The low-temperature application requires base oil with low viscosity while high-temperature grease requires highly viscous grease.
- Additive: Simple soap with calcium, lithium, and sodium as ingredients, complex soap, Additives are 0-10% in grease content. Additives in grease are used to enhance performance as well as give color to grease.
- Thickener: Used to thicken the grease contents. Thickeners are 5-20% or 5-30% of grease content.
Grease Penetrometer and consistency of grease
A grease penetrometer is a device utilized to determine the consistency of greases and similar materials. It measures the depth to which a standard needle or cone penetrates the grease specimen under standard conditions of temperature, time, and load. The penetration depth indicates the consistency of the grease, with softer greases allowing deeper penetration and vice versa. Consistency refers to the resistance of a material to deformation or flow. In the context of grease, consistency denotes its hardness or softness, which directly impacts its suitability for specific applications. Grease consistency is typically categorized into different grades, such as soft, medium, or hard, based on penetration depth measurements. The grease Penetration number (as per ASTM D217) is the depth in the tenth of a millimeter to which the prescribed weighted cone sinks into the grease sample. The higher the penetration number, the softer the grease, and the lower the penetration number, the harder the grease. The ASTM D217 standard outlines the procedure for determining the cone penetration of lubricating greases and related substances. It establishes the conditions for testing, including temperature, cone dimensions, and penetration depth measurements. Adhering to this standard ensures consistency and reliability in grease testing across different laboratories and industries. This article contains the content from ASTM D217.Steps to determine the penetration number of grease in the grease penetrometer setup
A penetrometer has a cone and needle which when allowed to fall in grease, the depth to which the needle goes into the grease is an indication of penetrometer and consistency which indicates the hardness of grease. The higher the consistency, the more the hardness of the grease and vice versa. The penetration is normally a tenth of a millimeter and indicates the penetration number.- A grease sample is placed in a grease container at a given temperature normally it is at room temperature.
- The standard cone (as per ASTM D217) with the given dimension and weight is allowed to fall into the sample container placed on the grease penetrometer table.
- Hold it for 5 seconds and measure the penetration.
- The distance to which the penetration is made is an indication of the penetration number. The lower the penetration, the harder the grease.
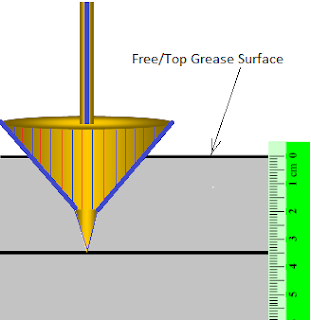
The penetrometer serves as an indispensable tool in grease analysis for several reasons:
Conclusion: The grease penetrometer, guided by the ASTM D217 standard, plays a vital role in evaluating the consistency of greases and similar materials. Consistency quantified through penetration number, serves as a critical parameter for quality control, formulation optimization, performance prediction, troubleshooting, and standard compliance in the lubricants industry. By employing penetrometer testing, manufacturers can ensure the reliability, performance, and longevity of grease products, thereby enhancing operational efficiency and minimizing maintenance costs in various industrial applications.
- Quality Control: Grease consistency directly influences its performance in lubrication applications. By accurately measuring penetration depth, manufacturers can ensure that greases meet specified quality standards and performance requirements.
- Formulation Optimization: Understanding the consistency of greases allows manufacturers to fine-tune formulations to achieve desired hardness or softness levels. This optimization process enhances product performance and longevity in various operating conditions.
- Performance Prediction: Penetration data obtained from the penetrometer aids in predicting the behavior of grease under different temperatures and load conditions. This information is crucial for selecting the appropriate grease for specific machinery or equipment to ensure optimal performance and longevity.
- Troubleshooting: In industrial settings, deviations in grease consistency can indicate potential issues such as contamination, degradation, or improper formulation. Regular penetrometer testing enables early detection of such problems, facilitating timely corrective actions to prevent equipment failure and downtime.
- Standard Compliance: Compliance with ASTM D217 or other relevant standards ensures consistency and comparability of test results across different laboratories and industries. It provides a common framework for evaluating and benchmarking grease consistency, fostering trust and reliability in the lubricants market.